A Guide to selecting the right Stepper Motor for your project
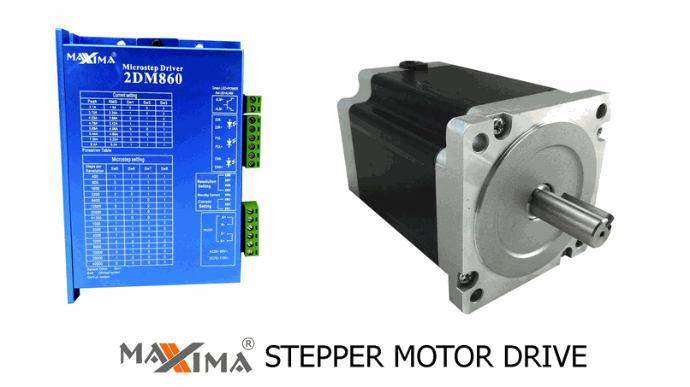
Stepper motors are a cornerstone in the realm of electromechanical systems, offering precise control over rotation angles and speed. Whether you're designing a 3D printer, CNC machine, or any other motion control application, choosing the right stepper motor is critical for the success of your project. With a myriad of options available, navigating through the selection process can be daunting. Fear not, as this guide aims to illuminate the key factors to consider when selecting a stepper motor.
- Understanding Stepper Motors: Before delving into the selection process, it's essential to grasp the basics of stepper motors. Unlike traditional motors, steppers move in discrete steps, with each step representing a fixed angular rotation. This characteristic makes them ideal for applications requiring precise positioning, such as robotics and automation.
- Torque Requirements: Determining the torque requirements of your application is the first step in selecting a stepper motor. Consider factors such as the load to be moved, frictional forces, and acceleration requirements. Ensure that the motor's holding torque exceeds the maximum torque required by your application to prevent stalling or missed steps.
- Step Resolution: Step resolution refers to the degree of angular movement per step. Higher step resolutions result in finer control but may require more complex driving electronics. Evaluate your application's precision requirements to determine the appropriate step resolution for your stepper motor.
- Speed and Acceleration: Stepper motors exhibit a trade-off between speed and torque. As speed increases, torque typically decreases. Additionally, consider the acceleration and deceleration profiles required for your application. Choose a motor with sufficient torque and speed capabilities to meet your dynamic performance criteria.
- Voltage and Current Ratings: Pay close attention to the voltage and current ratings of the stepper motor. Matching these ratings to your driver and power supply ensures optimal performance and prevents overheating or damage. Select a driver capable of delivering the required current while considering factors such as microstepping and current control mechanisms.
- Physical Size and Mounting: Consider the physical dimensions and mounting options of the stepper motor to ensure compatibility with your mechanical design. Factor in considerations such as space constraints, shaft diameter, and mounting hole patterns to seamlessly integrate the motor into your system.
- Environmental Considerations: Evaluate the environmental conditions in which the stepper motor will operate. Factors such as temperature, humidity, and exposure to dust or moisture can impact motor performance and longevity. Choose a motor with appropriate IP (Ingress Protection) ratings or consider additional protection measures if operating in harsh environments.
- Budget Constraints: While it's tempting to prioritize performance features, it's essential to consider budgetary constraints. Balance your project requirements with cost considerations to select a stepper motor that offers the best value for your investment.
- Future Scalability: Anticipate future developments and scalability requirements of your project when selecting a stepper motor. Opt for motors with room for expansion or those compatible with interchangeable components to facilitate future upgrades or modifications.
In conclusion, selecting the right stepper motor involves a careful evaluation of torque requirements, step resolution, speed, voltage, physical size, environmental considerations, budget constraints, and scalability needs. By understanding these key factors and conducting diligent research, you can confidently choose a stepper motor that meets the unique demands of your project, paving the way for smooth and precise motion control.